High Molecular Weight Methacrylate (HMWM) concrete sealer is a commonly specified material for filling cracks and eliminating porosity in the surface of concrete bridge decks. While the effectiveness of this material is generally proven for these goals, there is another benefit that sometimes goes unrecognized. Some HMWM is able to improve the stiffness of a concrete deck that has suffered from cracking.
While the chemistry behind the material may be very technical, the functionality of HMWM is simple; it fills cracks and saturates the surface of concrete as a liquid, then turns in to hard plastic blocking out moisture and chlorides. Not a coating that can wear off, or water repellent that leaves cracks unfilled, HMWM remains in the cracks and pores forever without degrading or disappearing.
Many more deck sealing options are available today, but at the time HMWM came to initial popularity in the early 1980’s there were two primary ways to seal bridge decks: Methyl Methacrylate and by epoxy injection. Each had their issues and downfalls, HMWM provided a solution that was necessary and timely. The effectiveness of HMWM to fill cracks and significantly reduce moisture and chloride ingress in bridge decks is more well known by engineers today, but a brief discussion of this seems warranted. California Department of Transportation (CalTrans) was an early adopter of HMWM technology, with increasingly widespread use throughout the early 1980’s. In 1984 they sealed the Benicia Viaduct bridge (just two miles from the current KBP headquarters) with HMWM through the dump and broom flood coat method. Five years later they took twenty cores from random locations, typically at the intersection of multiple cracks. All cores held together and no new cracks were found. Inspection with a microscope and ultraviolet light showed that the average depth of HMWM penetration exceeded 3 inches, and most were to the bottom of the core. A similar but more wide-spread investigation was completed in 2008/2009 by CalTrans, but this time of locations state wide, beginning with a gathering of 1,200 cores. This study tested a random subset of 100 of those cores, from 25 different installation contracts. The results showed the average crack penetration to be 86% of the crack depth, and 75% of the cracks had full penetration.
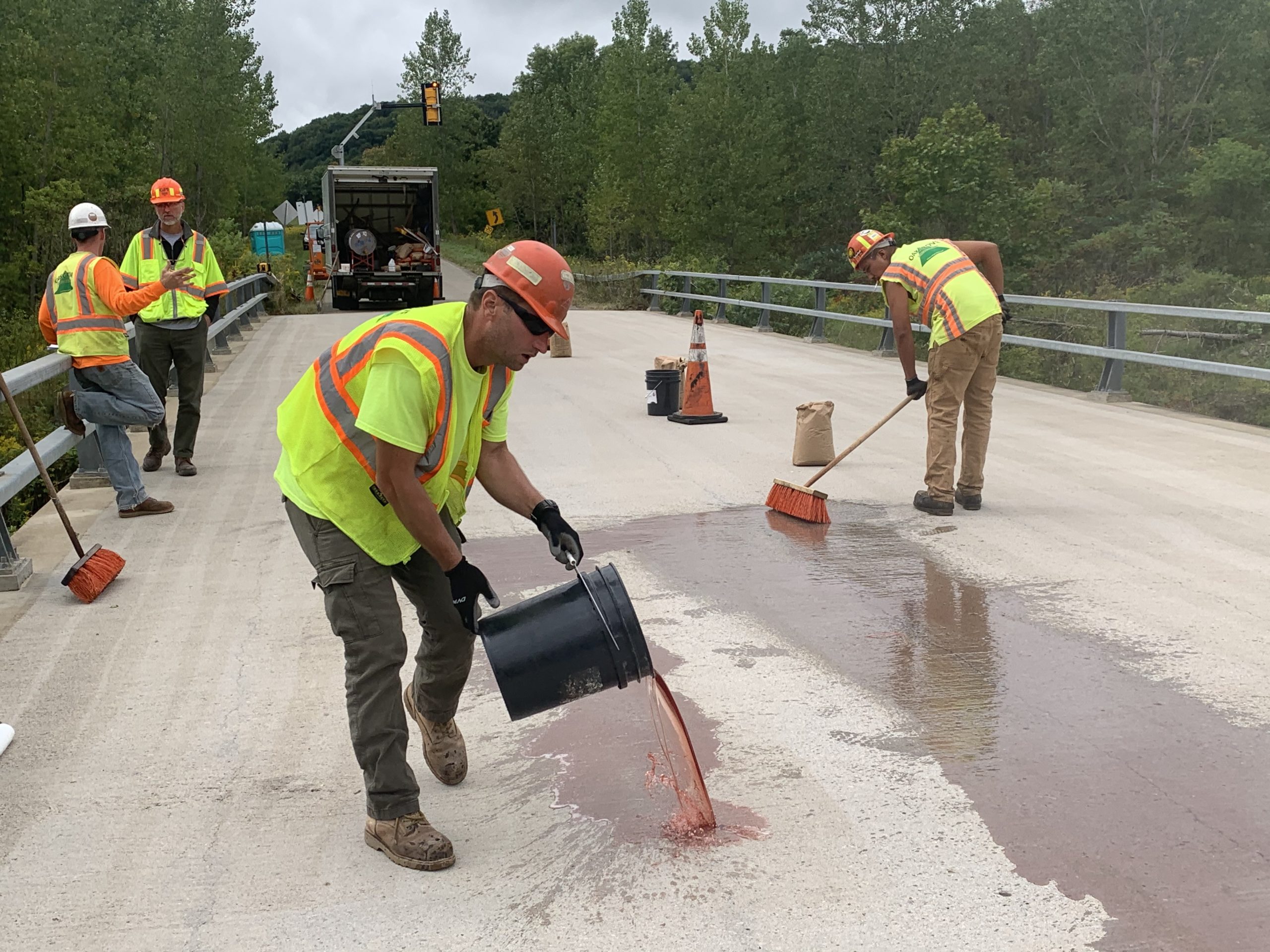
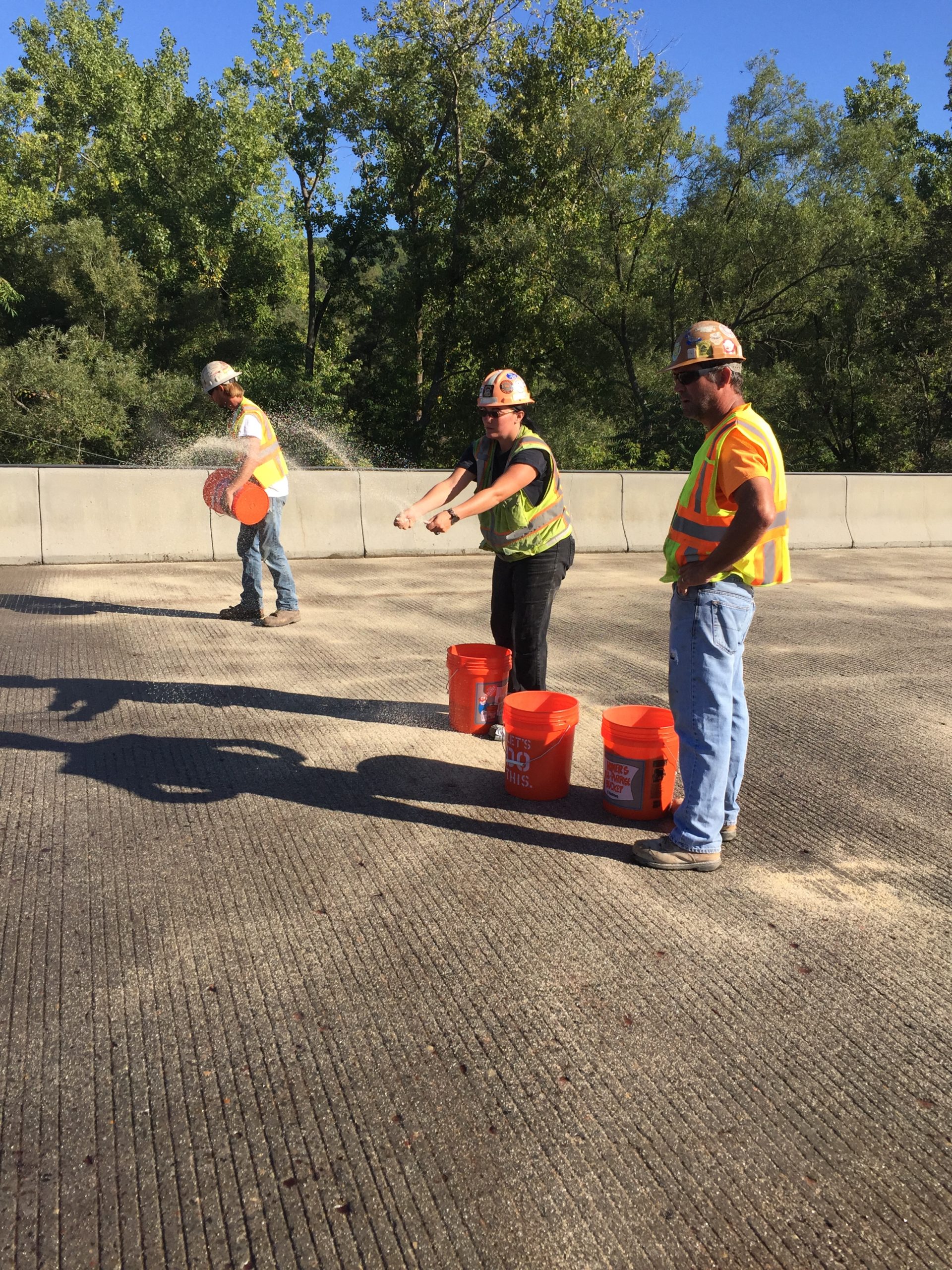
Many polymer-based sealers that fill cracks in concrete can be shown to keep out moisture and chlorides. However, those that are too weak or flexible will not provide the added benefit of improving structural stiffness. If a sealer were capable of filling the majority of a crack in concrete but only offered the consistency of bubble gum, one would not logically expect any change to the structural characteristics of the deck. Additionally, sealer properties measured at peak stress are generally regarded by those who understand material properties to be inconsequential when used against concrete. This is due to the stress required to achieve maximum elongation being many times greater than the tensile strength of the adjacent concrete. Sealer elongation that only occurs after 3,000 psi tensile stress is applied to it offers no benefit considering that the concrete it is placed against is only capable of withstanding under 500 psi of tensile stress. A sealer that is effective at stiffening a cracked bridge deck must offer only slightly more tensile elongation than zero when a realistic stress of 200-400 psi is applied. Our KBP 204 series of High Molecular Weight Methacrylate sealer features just that. Following the proven ability to fill even small cracks in bridge deck concrete, further research was conducted to substantiate and verify the materials ability to restore a cracked bridge deck to its original flexural stiffness.
The Western Transportation Institute at Montana State University was contracted by CalTrans to conduct research in the stiffening of cracked concrete bridges through the application of HMWM sealer (report CA14-1723). Our KBP 204 HMWM sealer was the material selected for the study. This research included testing of eight full-scale bridge deck panels (four sets of two panels each, 8.45 ft x 7 ft x 6.5 in) of various stages of deterioration. A 20 kip rolling wheel load was applied to simulate traffic and deteriorate the panels. Six of the eight panels were treated with our KBP 204 HMWM sealer at various traffic levels, with a total duration of 2,000,000 cycles. Two panels remained untreated as a control group. The performance of the treatment was evaluated based on the flexural stiffness of the panels at each given test time.
The final results of the stiffness testing were generally very positive, and some other interesting benefits were discovered. The HMWM was applied to the treated sets at approximately 25,000, 250,000, and 1,000,000 cycles of simulated traffic loading, and one set left untreated. It should come as no surprise that all of the test panels experienced cracking as the loading was applied. Interestingly, after the cracks were sealed, “only a few (or no) new cracks formed in the treated test panels under continued loading.” While this is not itself a factor in the stiffening of the concrete, it does attest to the effectiveness of our KBP 204 HMWM to permanently treat cracks without allowing any subsequent or adjacent re-cracking. It also implies that a surface treatment of our HMWM sealer actually reduces the propensity for cracking under loading. This is a powerful and under-recognized benefit offered by our KBP 204 HMWM sealer.
Flexural stiffness of the test panels most sharply declined in the early portion of loading, generally within the first 100,000 cycles. The stiffness continued to drop after that, but not as greatly, with the most gradual loss of stiffness after 250,000 cycles. Since only the top panel cracks were treated with HMWM, it would be impossible for the sealer to restore full original stiffness to the panels, and the results were consistent with this assumption. However, our KBP 204 HMWM sealer was able to increase the flexural stiffness in the cracked panels in all cases. The greatest increase in stiffness after HMWM treatment was shown in the panels that had the highest degree of cracking prior to treatment. This makes sense, after all there can be no benefit to a crack that hasn’t happened yet. Some panels saw as much as 10% increase in flexural stiffness after treatment, a monumental achievement for such a simple system.
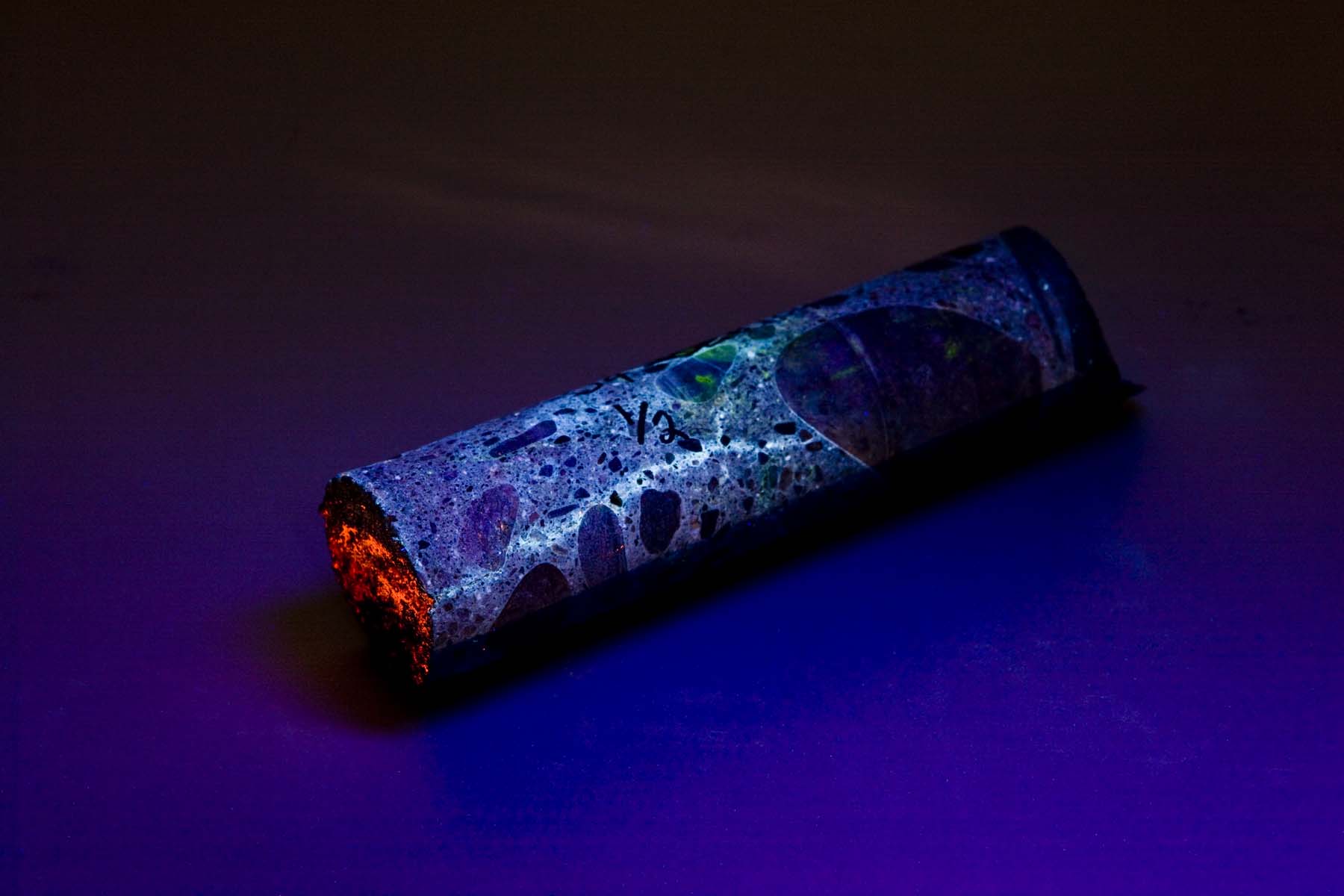
On the other side of the benefit of HMWM sealer treatment for flexural stiffness is the ability to maintain stiffness after application. One set of treated panels saw a decrease in stiffness of only 4% between about million and two million cycles. This could be primarily caused by bottom side cracking, as the samples showed little or no additional top cracking after HMWM treatment. The untreated panels, on the other hand, suffered a 34% loss of stiffness.
Other research has been performed to study the benefit of gravity-fill polymer crack sealers at stiffening concrete. Sprinkel and DeMars of the Virginia Transportation Research Council (VTRC) published a report in 1995 on Gravity-fill Polymer Crack Fillers. One urethane, three epoxies, and a High Molecular Weight Methacrylate (HMWM) were included in the testing. HMWM was the highest performing sealer in the study, offering 116% average stiffening in the beams. The research concluded that HMWM performed the best, however, the specific material involved in the testing had a strong, pungent odor and possible dangerous mixing procedure. Neither are issues with our KBP 204 P Seal HMWM sealer. One of the epoxies in the testing performed almost as well as the HMWM but had a long cure time, and twice the cost.
Stiffness restoration is not universal for all HMWM materials that are available, as found by previous research. In 1992 Michael Sprinkel (VTRC) published a report on the Use of High Molecular Weight Methacrylate Monomers to Seal Cracks in Bridge Decks, Retard Alkali-Silica-Aggregate Reactions, and Prime Bridge Surfaces for Overlays. Obviously, this research went further into the effectiveness of HMWM for more than just stiffening, as the title implies. This research found no increase in flexural strength through application of HMWM sealer. However, this may be a function of crack filling ability, as the sealer involved in his testing did not fill cracks very well at depths greater than 0.5 in from the surface.
Concrete cracks. That’s nearly as guaranteed as death and taxes. Bridge decks depend on stiffness to maintain their load capacity. Our KBP 204 family of HMWM sealer is not only proven to preserve bridge deck concrete by sealing out moisture and chloride, but can be considered as a tool for restoring and maintaining flexural stiffness.
Sources:
High Molecular Weight Methacrylate Resins in California. CalTrans report published January 7, 1991, Henry Jerzak
Analyses of Selected Cores (sic) Samples Evaluated for Methacrylate Crack Penetration (Phase II Report). CalTrans publication November 19, 2010, Robert A. Reis, P.E.
Investigation of Methacrylate Rehabilitation Strategy to Extend the Service Life of Concrete Bridge Decks. CalTrans Report Number CA14-1723, September 2013, Eli Cuelho and Jerry Stephens
Gravity-Fill Polymer Crack Sealers. Transportation Research Record 1490, July 1995, Michael M. Sprinkel and Mary DeMars
Use of High Molecular Weight Methacrylate Monomers to Seal Cracks in Bridge Decks, Retard Alkali-Silica-Aggregate Reactions, and Prime Bridge Surfaces for Overlays. Transportation Research Record 1347, 1992, Michael M. Sprinkel.