We often get asked about deck repair (patching) materials during design as well as the pre-construction phase of a project. We see a wide array of successes and failures related to patching work performed ahead of an overlay, and are glad to share our suggestions for best practices.
Most often, the question we are asked has to do with how much patch material cure time will be required for our Polyester Polymer Concrete (PPC) system to adhere. This is easy to address, but does not actually cover all of the factors that contribute to successful deck repair and overlay compatibility, or even its success on a bare deck that’s not receiving an overlay. Once a cementitious patch material is completely dry at the surface and achieves the required tensile strength to pass adhesion tests (typically 250 psi), our PPC can bond and cure properly. This simple approach does not assure overall success, as other factors have more impact than just strength. That being said, some further guidance for timing of overlay placement on cementitious patch materials can be found on our Product Data Sheets. Generally, this calls for patches made with most cementitious materials to reach both 80% expected ultimate strength AND a minimum of 3-days open air cure after wet-curing prior to overlay.
The other question we are asked most often about deck repair materials has to do with which one we recommend. This is much easier as we have seen near universal success with the use of our PPC system as a deck repair material prior to overlay, as well as when used for bare deck repairs. Our PPC has been developed and refined to maintain a careful balance of properties that are important to maintaining compatibility with the surrounding bridge deck, the forces applied under traffic, and the deflections and thermal movements typical of bridge decks. When presented with a list of lab-evaluated approved list deck repair materials, we often struggle to find one that has shown to be effective as a deck repair material prior to application of a polymer overlay. This brings us back around to suggesting what we know works, our PPC.
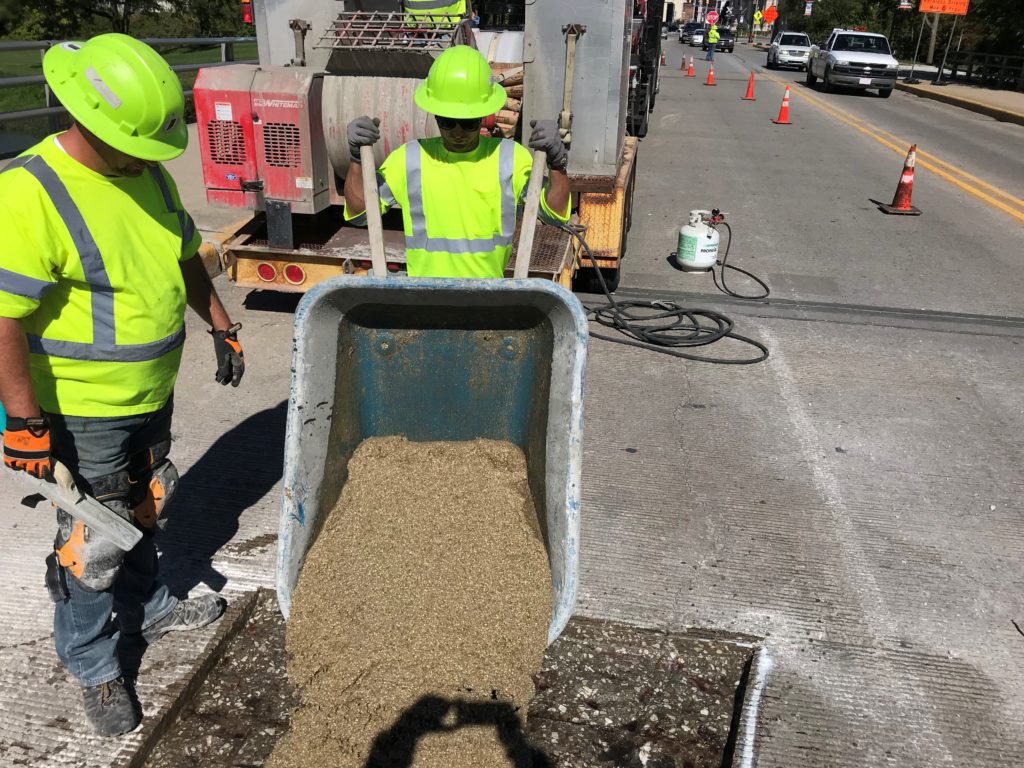
KBP PPC 1121 placement prior to overlay application.
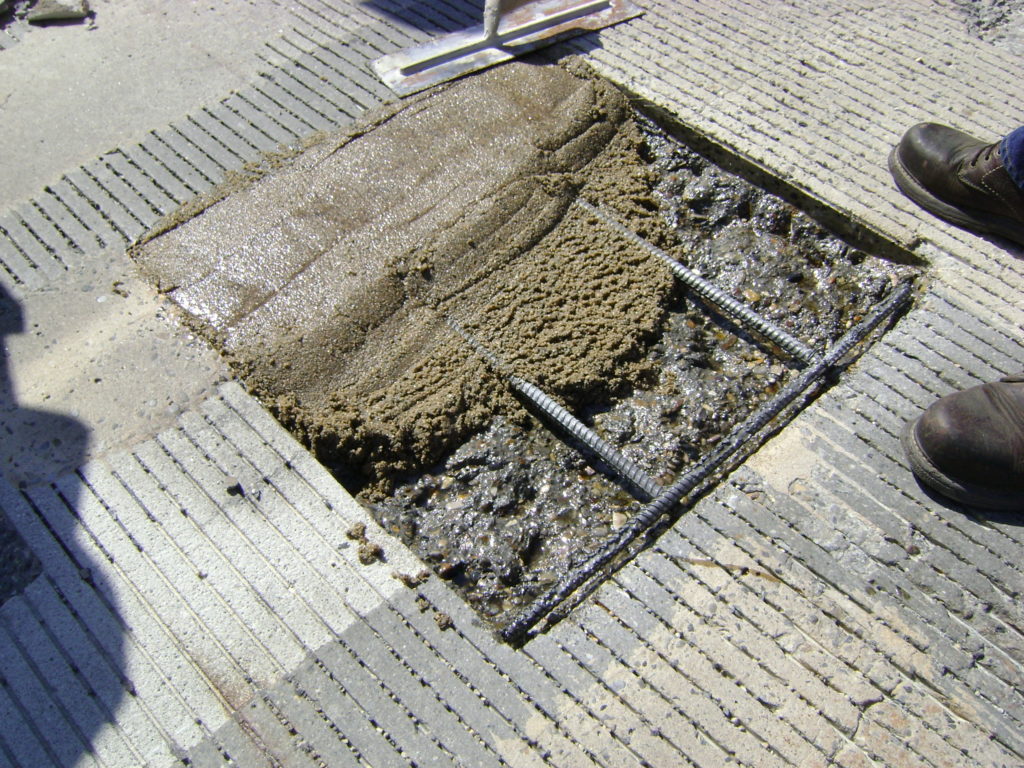
KBP PPC 1121 during patch installation.
Many properties can be considered when selecting a bridge deck repair material. For the sake of this guidance, we will move past the most basic, obvious properties and focus on the few that are most contributory to the success or failure in the patching application. For example, it is obvious that a certain minimum compressive strength should be achieved by a repair material for structural sufficiency, and that any strength achieved beyond that of the surrounding deck concrete is superfluous. Instead of the obvious compressive strength achievement, we will focus this guidance on other often overlooked properties like total shrinkage, Coefficient of Thermal Expansion (CTE), and Youngs Modulus (Modulus of Elasticity, MOE). Interestingly, many of the properties that are deficient in some patching materials are actually converted to advantages in our PPC system, more so in our HCSC, through a carefully balanced optimization of properties.
Shrinkage during the curing period can cause issues both shortly after placement, and long after the patch is in service. All polymer bridge deck overlays are designed to adhere to substrate concrete. Most do this very well just after installation. Those with properly balanced thermal and elastic properties are able to remain bonded for a very long time, or even permanently. This is certainly a great advantage of properly designed polymer overlays. However, if shrinkage in a substrate deck repair material exposes any appreciable separation either at the patch/deck interface or as a crack within the patch, the separation is likely to reflect up through the bonded polymer overlay. This reflected crack opens up a pathway for moisture and chloride intrusion into the substrate deck, which works against the full potential and benefit of the polymer overlay. At this point, the small savings on cheap bag-mix concrete for substrate repair turns into a long-term detriment to the longevity of the bridge. On the other hand, if the shrinkage of the patch is complete prior to overlay installation, our KBP 204 family of HMWM primers and sealers can act to fill the voids created by the use of a less than ideal repair material. It seems obvious that a more suitable repair material would be advantageous, but as backup insurance our primer can help seal in the failures of lesser options.
Most cementitious materials report their linear shrinkage. Considering the typical rushed timeline of bridge preservation projects though, decision makers should carefully evaluate the period in which that shrinkage was measured. This property is often reported as the shrinkage that occurs between 24 hours and 28 days after initial set. The point during cure that the initial measurement is taken is arguably just as important as the number that is reported. If appreciable shrinkage occurs in the time from initial set to 24 hours later, then the data given from the period after that is substantially incomplete. Additionally, if the total shrinkage is reported as of a full 28-day cure, it would be impossible to discern when that repair material could be trusted to receive an overlay at any time prior to 28 days. Proper decision making must be based on the anticipated shrinkage both before and after the time the overlay is to be applied. As discussed earlier, depending on our KBP 204 family of HMWM primer/sealers to fill edge voids caused by shrinkage is a sound back-up plan, but quality patch material selection would be preferred.
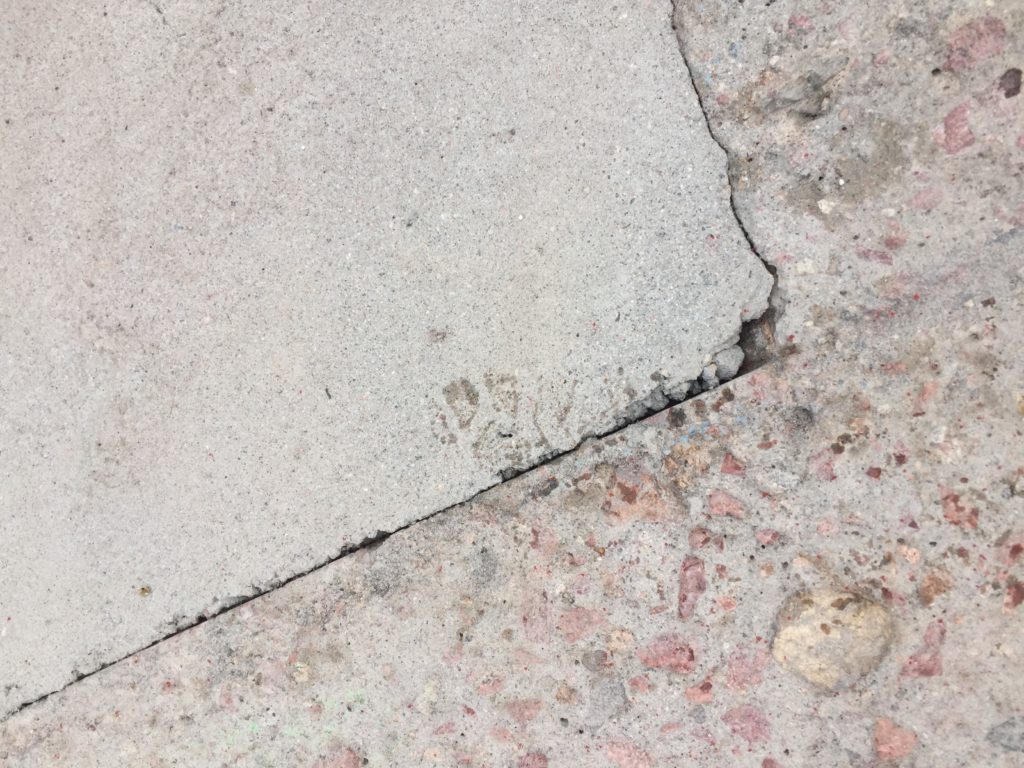
Separation from surrounding concrete due to shrinkage of patch material.
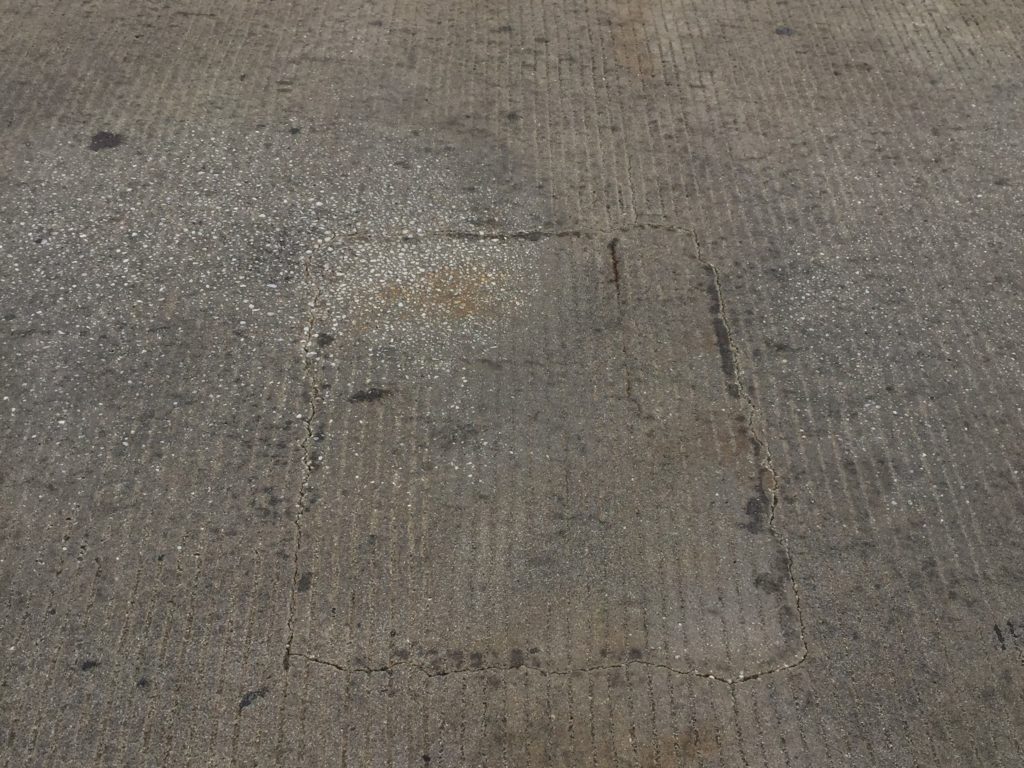
Cracked through bonded polymer overlay, above patch/deck interface, resulting from substrate patch deficiency.
Low or no total shrinkage materials can help avoid this initiation of failure in bridge deck repair. Other solutions, like with our PPC and HCSC systems, can come from carefully developed curing order at the bond interface, as well as in the tensile strength development timing vs. shrinkage force development. If a high shrinkage cementitious material is selected for use prior to a polymer overlay, careful evaluation of the timing of shrinkage should be taken to minimize the risk of separation reflecting up through the bonded overlay.
Individual properties are important. But some properties can have less effect or be made significantly more influential when balanced with others. For example, Coefficient of Thermal Expansion (CTE) can either match the surrounding concrete, or be balanced out by a lower Modulus of Elasticity (MOE). Traditional cementitious concretes follow the “match like with like” path to thermal compatibility. Some more advanced cementitious materials achieve very high compressive strengths, but this often also comes with high CTE and high MOE. This combination can lead to ultra high bond line stresses and inevitable failure in the weaker adjacent material. A material with this combination of high strength, CTE, and MOE should be avoided as a bridge deck repair (or overlay).
Polymer-based concrete repair materials are very broad in their components, design, and properties. Resin properties are important, but no more important than resin content within the mix. Unless the resin content required to balance with the aggregate filler system is very low, the CTE of the mixed system will be very high. In general, CTE greater than two times that of the surrounding concrete will lead to very early crushing or tensile failure within the adjacent concrete. However, any material with CTE greater than the surrounding host concrete should be balanced out with MOE lower than that of the adjacent concrete. The greater the difference between thermal properties of adjacent materials, the lower the Modulus should be. However, if the MOE is low enough it could suffer early wear or even lack structural stiffness. Out of balance polymer concrete repair materials are commonly available and often pass lab-based evaluation for approval. They get hard, they pass a simple evaluation, then they tear apart the bridge deck around them when actually used. When called to explain, the excuse given by vendors is often that the surrounding deck wasn’t strong enough to receive a repair. This is simply not true. It is not the bridge decks fault that it can’t hold a patch in place that imposes extreme tensile stresses during normal thermal cycles. Not all materials are suitable for bridge deck patching. If the properties cause failure in an outside natural setting, they should be avoided.
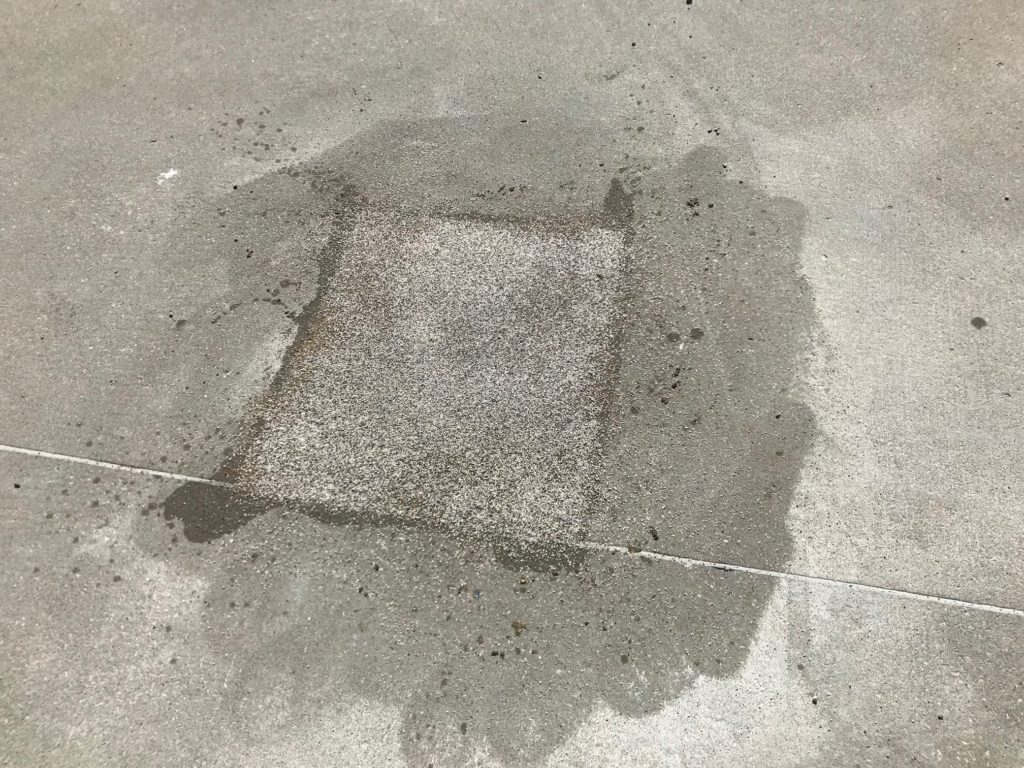
KBP PPC 1121 patch after installation.
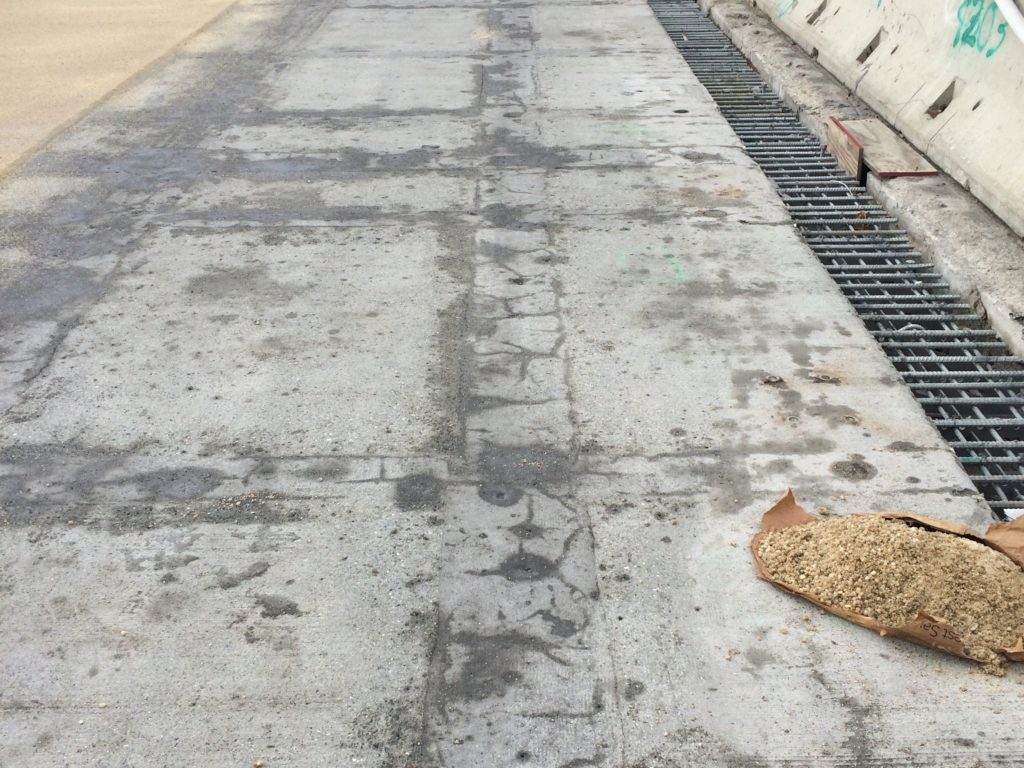
Intermediate and edge interface cracking of CIP deck infill material. Closure pour application shown, similar performance could be expected if used for deck repairs.
Kwik Bond PPC on the other hand, has been carefully developed and refined to achieve a successful balance of strength, CTE, and MOE. Our long history of success in this application is a strong testament to the balance of properties. Our PPC system is designed to have a relatively low resin demand, but more importantly the individual component properties and compatibility yield a favorable mix of final composite properties. CTE less than two times that of typical bridge deck concrete coupled with MOE under 2,000 ksi gives a glimpse into the successful balance we have achieved. Other properties come into play as well, like transition zone strengthening and integrated chemical bond achieved through the use of our KBP 204 family of HMWM primer. There are no exact replicas of our PPC system available. Less successful polyester based systems often fail due to improper binder resin tensile properties, lack of protection from hydrolysis, incompatibility between HMWM primer and polyester binder resin, curing order that is out of sync with strength development and shrinkage, and much more. These are all issues that have been solved through the development of our PPC 1121 Polyester Polymer Concrete system.
Bridge decks are not easy to repair. Live load deflection and vibrations, thermal movement, rapid return to service, and other factors make bridge construction more difficult, and material selection more critical. The simple bag-mix materials that may work successfully in a more thermally and mechanically static application aren’t necessarily appropriate for bridge work. Our PPC 1121 Polyester Polymer Concrete system has been carefully developed and refined to achieve long lasting success as a bridge deck repair and overlay system. Properties that are sometimes overlooked can be critical to the outcome and success of a repair strategy.
A few summary points for patch material selection:
- Use KBP PPC or HCSC for maximum efficiency, effectiveness, longevity, and compatibility.
- If selected based on passing a thorough evaluation, traditional cementitious concrete should reach over 80% of ultimate strength (not just design strength) AND a minimum of 3 days open air drying after wet cure prior to overlay.
- If cementitious concrete repair materials are to be used, select those with little or no expected shrinkage. Pay close attention to total shrinkage, not just what takes place after a late initial measurement.
- Select materials that have all properties optimized for success, not just strength. Coefficient of Thermal Expansion, Modulus of Elasticity, and interface treatment are just as important.
For more in-depth discussion, or to hear what our proven materials can offer to solve bridge preservation issues, please feel free to reach out to our team of experts. Long lasting, or even permanent bridge repair and preservation materials are available. Look beyond the basic properties, understand what makes materials truly compatible with their surroundings, and do what is best for your bridges.